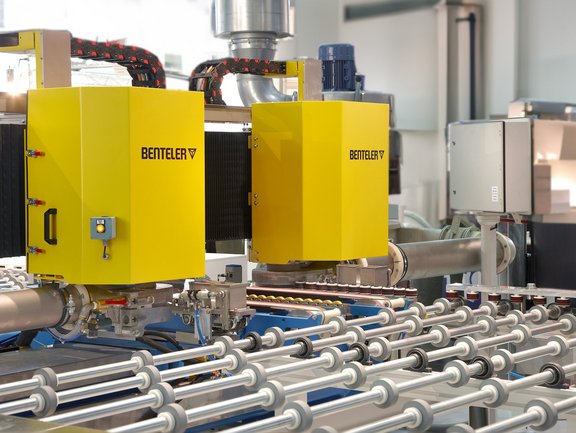
Grinding Machines
The BENTELER flat glass grinding machines convince due to their optimal grinding results based on precision, speed and process reliability.
Glass grinding machines
Accuracy, speed, and process reliability form the foundation of BENTELER Glass Processing Equipment's flat glass grinding machines—ensuring optimal grinding results. Additionally, with fast, automatic width and glass thickness adjustments, we guarantee high flexibility and short cycle and setup times for all edge types. Efficient solutions for every challenge!
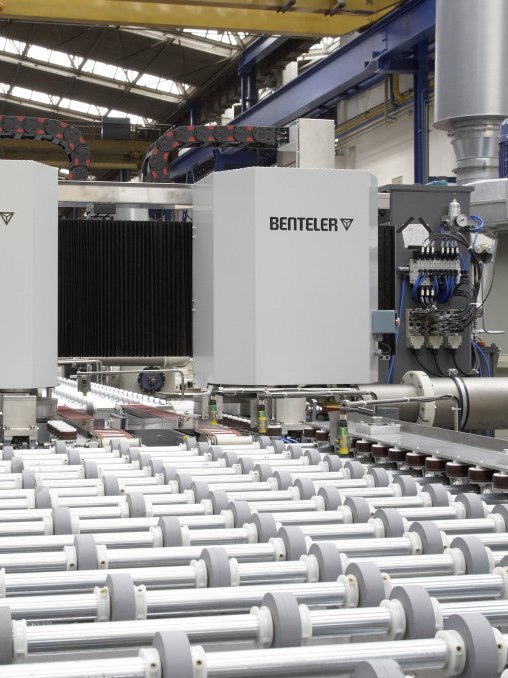
This patented grinding machine stands out by extremely high availability. A high speed cooling water extraction guarantees a dry and clean grinding line. With easier handling and high automation, the tool change is carried out in just a few minutes.
Advantages
High availability:
- Semi-automatic tool change
- Automatic tool measuring
- Automatic tool sharpening
- Automatic wear compensation
- Dry and clean grinding line due to high speed cooling water extraction
Improved product quality:
- High grinding spindle performance for maximum grinding speed
- Optimized closed cooling ring - Absence of cooling water on the glass surface
- Automatic tool adjustment and wear compensation
- Glass fixing by vacuum belts for grinding without touching the glass surface
Low total cost of ownership by:
- The same processing tool for both glass edge and corner
- Reduction of downtime
- Wear parts in dry and clean environment
- Maximization of uptime
Reduction of maintenance-time
Technical data | Fields of application |
---|---|
|
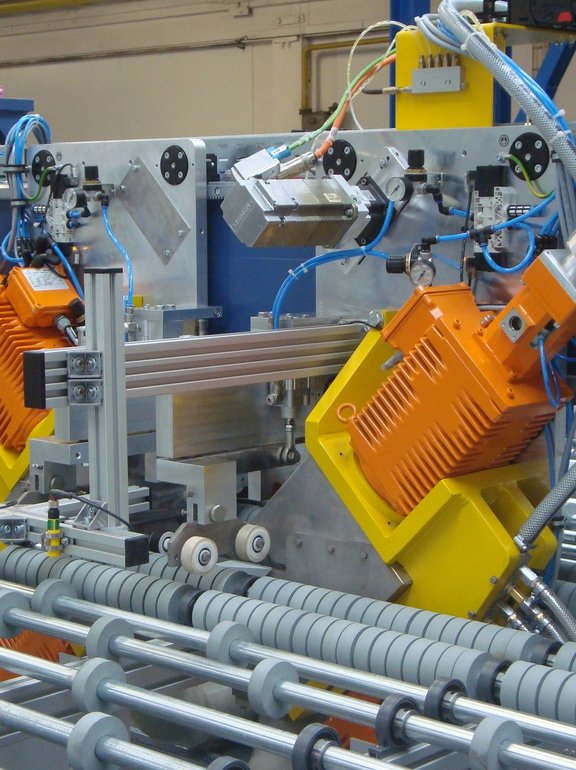
Achieving fast cycle times with minimal tool wear characterizes our Seamer. Our machine concept combines high durability of grinding tools, short set-up times and precise edges. The Seamer is particularly used in the ESG-Manufacturing.
Advantages
High precision:
- Grinding spindles with linear adjustable rotor for seaming
- Smooth and precise edges
Flexibility:
- Compact design
- Short set-up times
- Optional with a water filtration system
Process safety:
- Long lifetime by seaming with cup-wheels
- Effective exhaust fans with noise protection
- Completely enclosed wet area
- Nearly dry glass after seaming, through cooling water extraction
- No leaking of water
Simple, comfortable operation:
- Precise and fast width adjustment 60 m/min
Easy and precise setting of seaming sizes
Technical data | Fields of application |
---|---|
| Architectural Glass |

The BENTELER standard Pencil-Edge Grinding Lines convince due to their optimal grinding results based on precision, speed, and process reliability. The very robust design of the Pencil-Edge Grinder makes longterm work possible (24/7) and has proven to be especially economical.
Advantages
High precision:
- Good grinding results also for large raw glass tolerances
- Machine frame and components of especially stable design for low vibration glass processing
- Precise width adjustment with fully automatic support bars for the exact positioning of the glass edges, also for large glass widths
Flexibility:
- Up to five grinding spindles for each side, therefore more flexible setup with a large application range
- Flexible design with a wide range of application
- Optional with an automatic glass thickness adjustment
Process reliability:
- Completely encapsulated high-precision grinding spindles with long service life in wet and abrasive environments
Simple operating:
- Automatic side and angle orientation to prevent unground glass surfaces and burns
Two synchronous motors for the transport and pressure belt support of each spindle for exact glass carriage and for rapid belt exchange
Technical data | Fields of application |
---|---|
|
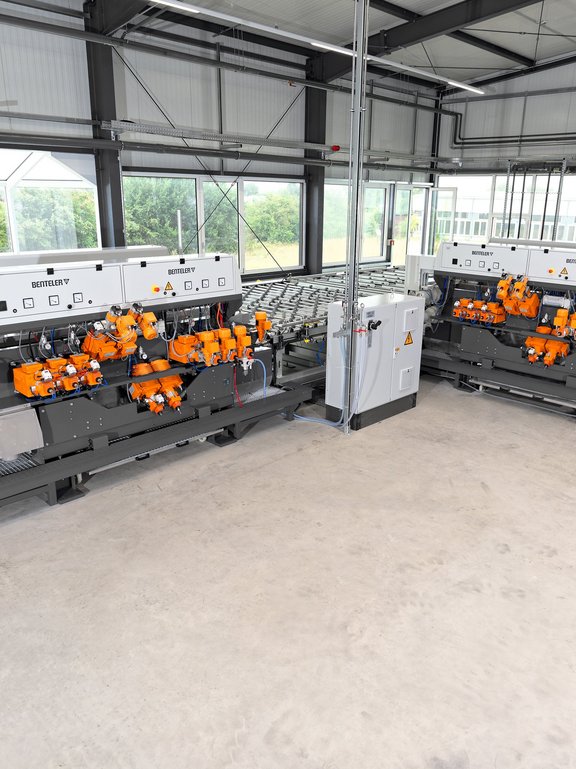
The BENTELER tecGrinder satisfies with short set-up times due to rapid width and automatic glass thickness adjustment. Your solution for flexibility, high process reliability and speed for all K-edge contours. The tecGrinder can be linked with an automatic handling system and a washing machine to a complete processing line, to avoid the handling in the manufacturing and to minimize cycle times. Your solution for flexibility, high process reliability and speed for all K-edge contours.
Advantages
High precision:
- Optimal grinding results up to 14 stations for each side for grinding and polishing of edge and seam
- Automatic side and angle alignment
- Solid machine frame and robust components
Flexibility:
- Automatic glass thickness adjustment
- Rapid and precise width adjustment
Process reliability:
- Completely encapsulated high-performance grinding and polishing spindles
- State-of-the-art machine control - Simple operating and menu guidance
- Evaluation of operating costs through an integrated data acquisition system
Simple operating:
- High working speed
Technical data | Fields of application |
---|---|
| Architectural Glass |
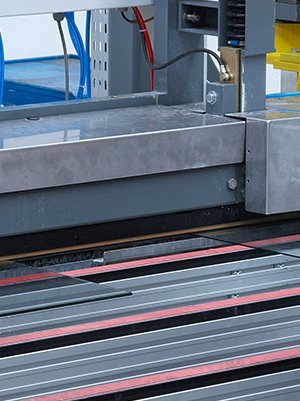
Do you process different glass dimensions or do you produce glass lites with different edge processing, every day? BENTELER provides you with the One-Side Grinding Machine, a machine on which you can process glasses of different width and shape in direct sequence. And this is without set-up times and without idle and adjustment times. In addition, our innovative system demonstrates with constant quality at a high throughput.
Advantages
High precision:
- Works from loading to off-loading automatically
- Automatic alignment for dimensional and angular accuracy
- High and constant edge quality like a double-sided grinding machine
Flexibility:
- Up to 11 individual tool stations
- Perfect for production of a large range of models: Different widths can be processed in direct sequence - Processing of not rectangular glasses also possible
- Grinding, seaming and polishing in one process - Expandable to a grinding-drilling-washing-line
High efficiency:
- No set-up times, elimination of idle and adjustment times
- Use of our proven and robust spindle carrier
- High throughput due to short cycle times
- Simplified the operating processes
Technical data | Fields of application |
---|---|
| Architectural Glass |